Why do we need to connect Fatek PLC?
There are several reasons why you might need to connect a Fatek PLC to other devices:
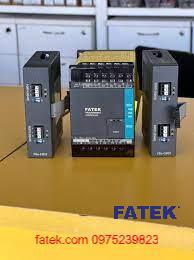
Data Exchange and Monitoring
- Human-Machine Interface (HMI): Connecting a Fatek PLC to an HMI allows operators to monitor and interact with the control system. The HMI can display real-time data from the PLC’s inputs and outputs, visualize process variables, and provide control interfaces for operators.
- Supervisory Control and Data Acquisition (SCADA) System: A SCADA system can connect to multiple PLCs, including Fatek models, to monitor and manage a larger control network. This allows for centralized data collection, alarm management, and historical data analysis.
Control and Communication
- Multiple PLCs: In complex automation systems, you might need to connect multiple Fatek PLCs to coordinate actions and share data. This allows for distributed control, where each PLC handles a specific portion of the process, but they communicate to ensure overall system operation.
- Other Devices: Fatek PLCs can connect to various devices besides HMIs and SCADA systems. Examples include:
- Drives and motors for controlling variable speed machinery
- Temperature controllers for regulating industrial processes
- Networked sensors and actuators for expanding I/O capabilities
Benefits of Connecting Fatek PLCs
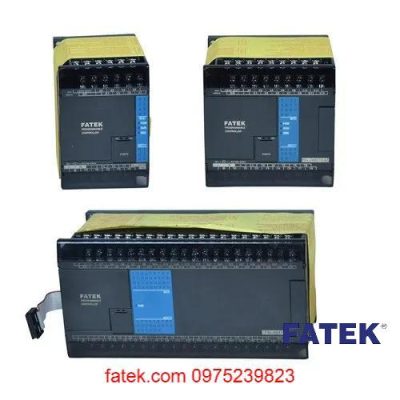
- Improved Control and Monitoring: By connecting PLCs, you gain a centralized view of your automation system, allowing for better process control, faster troubleshooting, and optimized decision-making.
- Scalability and Flexibility: Connecting PLCs allows you to expand your control system as your needs evolve. You can add new devices or integrate with existing systems for increased functionality.
- Remote Access and Management: Communication enables remote monitoring and control of your automation system. This allows for faster response times to issues, improved maintenance efficiency, and potential cost savings.
Popular Fatek PLC connection methods
Here are some of the popular connection methods for Fatek PLCs:
Serial Communication
-
RS-232: This is a widely used standard for serial communication over short distances. It’s suitable for connecting a Fatek PLC to a computer for programming or a simple HMI for basic monitoring. However, limitations include slower data transfer rates and limited cable lengths.
-
RS-485: This variant of serial communication offers several advantages over RS-232. It allows for multi-drop configurations, meaning you can connect multiple devices (up to 32) to a single PLC using a single cable. Additionally, RS-485 offers longer cable lengths compared to RS-232, making it suitable for connecting PLCs spread across larger distances.
Ethernet Communication
-
Ethernet/IP: This is a common industrial Ethernet protocol widely used for connecting various automation devices. It offers high data transfer rates and ease of network integration. Ethernet/IP allows for connecting Fatek PLCs to HMIs, SCADA systems, other PLCs, and various industrial devices on a standard Ethernet network.
-
Modbus TCP/IP: This is another popular Ethernet-based communication protocol for industrial automation. Similar to Ethernet/IP, it offers high data transfer rates and network integration. Modbus TCP/IP is a good choice if you need to connect your Fatek PLC to existing systems using the Modbus protocol but want the benefits of an Ethernet network.
Fieldbus Networks
PROFIBUS: This is a widely used fieldbus network for industrial automation applications. It offers high data transfer rates and deterministic communication, ensuring predictable response times. While not as common as Ethernet-based protocols, PROFIBUS might be required for specific applications or integration with existing systems using this protocol.
Instructions connect Fatek PLC to the computer
- Prepare software: Install Fatek WinproLadder PLC programming software on the computer.
- Cable connection: Connect the RS-232 cable or USB cable from the PLC to the computer.
- Configuration settings: Configure the connection port in WinproLadder software.
- Check connection: Test connection using the ping command or the connection test tool in WinproLadder software.
Instructions connect Fatek PLC to HMI
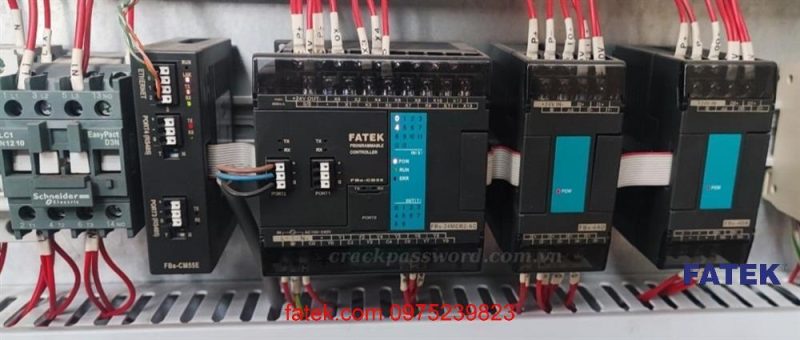
Connecting a Fatek PLC to an HMI (Human-Machine Interface) typically involves several steps. Here’s a general guide:
- Choose compatible hardware: Ensure that both your Fatek PLC and HMI are compatible and support the necessary communication protocols. Fatek PLCs usually support various communication protocols such as Modbus RTU, Modbus TCP/IP, or Fatek’s own communication protocol.
- Physical connections: Connect the Fatek PLC and the HMI physically using appropriate cables. This could involve RS-232, RS-485, Ethernet, or other communication cables depending on the supported interfaces of your devices.
- Configure communication settings on the PLC: Access the programming software for the Fatek PLC and configure the communication settings. This typically involves specifying the communication protocol, baud rate, data format, and addressing information. Refer to the user manual or documentation provided by Fatek for detailed instructions on configuring communication settings.
- Configure communication settings on the HMI: Access the configuration interface of the HMI and configure the communication settings to match those of the Fatek PLC. This includes specifying the communication protocol, baud rate, data format, and addressing information. Refer to the user manual or documentation provided by the HMI manufacturer for detailed instructions on configuring communication settings.
- Develop HMI screens: Use the HMI software to design and develop the graphical user interface (GUI) screens for interacting with the Fatek PLC. This involves creating buttons, indicators, data entry fields, and other graphical elements to display and control PLC data.
- Map PLC tags to HMI elements: Within the HMI software, map the PLC memory addresses or tags to the corresponding elements on the HMI screens. This allows the HMI to read data from the PLC and update the graphical elements accordingly, as well as send control commands from the HMI to the PLC.
Instructions for connecting Fatek PLC to I/O devices
- Select communication protocol: Select the appropriate communication protocol for the I/O device, such as Modbus or Ethernet.
- PLC Configuration: Configure the PLC to use the selected communication protocol.
- Configure I/O devices: Configure I/O devices to connect to the PLC and transmit data.
- Check connection: Check connection using public
Communications
FATEK VIETNAM COMPANY
Website: https://fatek.com.vn/
Hotline: 097 523 9823