What is Servo Fatek?
Servo Fatek refers to two interconnected elements within the FATEK Automation Corporation’s industrial automation product line:
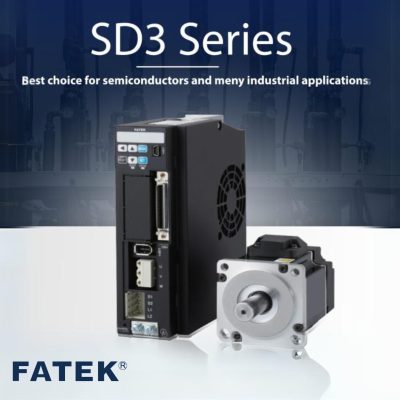
-
FATEK Servo Drives: These are electronic drives designed to control AC or DC servo motors with high precision. Servo motors offer precise control over speed, position, and torque, making them ideal for various industrial automation applications requiring accurate movement. FATEK servo drives come in various power ratings and functionalities to suit diverse application needs. They communicate with control systems (PLCs, HMIs) using various communication protocols, including RS-485.
-
Servo Studio SD3 Fatek Software: This is a dedicated software application specifically designed for configuring, operating, and monitoring FATEK’s SD3 series servo amplifiers. The software provides a user-friendly interface for:
- Configuration: Setting up motor parameters (type, encoder resolution), control mode (position, velocity, torque), gains (for performance tuning), and safety limits.
- Operation: Sending control commands to the servo drive (target positions, velocities, or torques) and monitoring the motor’s behavior in real-time.
- Monitoring: Visualizing and analyzing key servo data like position, speed, current, and voltage. This data is crucial for troubleshooting, performance optimization, and ensuring safe operation.
- Data Recording and Analysis (Optional): Some versions might offer functionalities to record servo data for later analysis, helping identify trends, diagnose issues, and further refine control strategies.
Outstanding features of Servo Fatek
Servo Fatek, which combines FATEK servo drives and Servo Studio SD3 Fatek software, offers a range of features that contribute to precise and efficient control of AC or DC servo motors in industrial automation applications. Here’s a breakdown of the key highlights:
FATEK Servo Drives
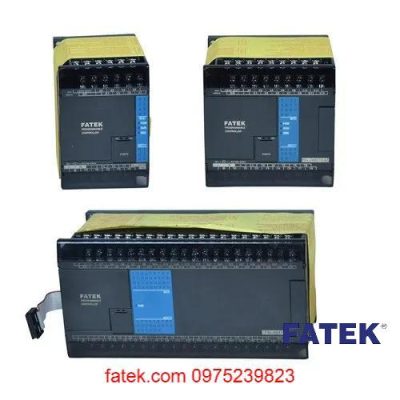
- Precise Motor Control: Deliver high-precision control over motor speed, position, and torque. This enables accurate movement profiles and consistent performance in applications like CNC machining, robotics, and material handling.
- Variety of Models: Available in various power ratings and functionalities to cater to diverse application needs. From low-power options for delicate tasks to high-power drives for heavy-duty industrial machinery.
- Communication Options: Support various communication protocols, including commonly used RS-485, for seamless integration with different control systems (PLCs, HMIs) within an automation network.
- Overload Protection: Often incorporate built-in overload protection features to safeguard the motor and drive from potential damage during operation, promoting system reliability.
Servo Studio SD3 Fatek software
- Simplified Configuration: Provides a user-friendly interface for setting up and configuring parameters of the SD3 servo amplifier. This reduces programming complexity compared to manual methods.
- Enhanced Performance Tuning: Offers functionalities for adjusting control loop gains (proportional, integral, derivative) to optimize servo performance for specific applications. This leads to smoother motion control, improved accuracy, and faster settling times.
- Real-time Monitoring: Enables real-time visualization of crucial servo data like position, speed, current, and voltage. This data provides valuable insights for:
- Troubleshooting: Identifying potential issues and diagnosing problems that might arise during operation.
- Performance Analysis: Monitoring and analyzing servo behavior to assess control effectiveness and identify areas for further optimization.
- Safe Operation: Ensuring the servo motor operates within safe parameters and limits to prevent damage or accidents.
- Data Recording and Analysis (Optional): Some versions might allow recording servo data over time. This data can be analyzed later to:
- Identify trends: Monitor changes in servo performance over time and detect potential issues before they become critical.
- Diagnose recurring problems: Analyze historical data to pinpoint the root cause of recurring issues.
- Refine control strategies: Leverage data analysis to continuously improve control loop tuning and optimize performance for specific applications.
Choose the right Fatek servo for application
Choosing the right FATEK servo drive for your application involves carefully considering several factors to ensure optimal performance and successful implementation. Here’s a breakdown of the key selection steps:
Identify application requirements
- Motor Type: Specify whether you require an AC servo motor or a DC servo motor. AC motors offer higher efficiency and wider speed ranges, while DC motors might provide higher torque at lower speeds.
- Power Requirements: Determine the continuous and peak power (watts or horsepower) needed for your application’s movements. Consider factors like motor size, load inertia, and desired acceleration rates.
- Torque and Speed Range: Identify the required torque (Nm or lb-ft) and speed (RPM) range for your application. This will influence the motor’s selection and potentially the needed gearbox ratio.
- Control Mode: Decide whether you need position control (precise positioning of the motor shaft), velocity control (maintaining a constant speed), or torque control (regulating the motor’s output torque).
- Communication Protocol: While RS-485 is a common choice, some applications might require different protocols (e.g., Modbus TCP) for integration with your control system (PLC, HMI).
- Environmental Conditions: Consider factors like operating temperature, humidity, and vibration levels within your application environment. Some servo drives might be better suited for harsh environments.
Explore FATEK Servo drive catalog
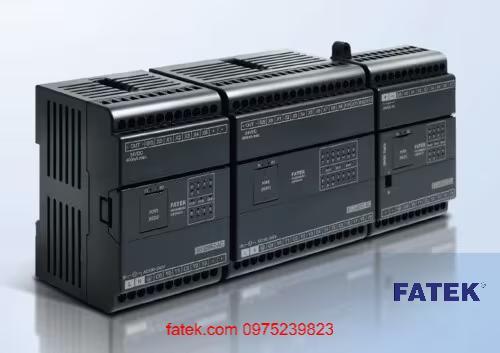
Refer to the FATEK Automation Corporation website or distributor catalogs to browse their range of servo drives. Utilize filters based on power ratings, motor types, control modes, and communication protocols to narrow down your options.
Evaluate Servo drive specifications
For shortlisted servo drive models, carefully review their technical specifications, including:
- Power ratings (voltage, current)
- Continuous and peak torque outputs.
- Speed range (RPM).
- Encoder resolution (pulses per revolution).
- Supported control modes.
- Communication protocols.
- Physical dimensions and weight.
Fatek servo application solution
FATEK drives, combined with Studio SD3 Fatek software, offer a comprehensive solution for various industrial automation. Applications requiring precise control of AC or DC servo motors. Here are some examples of how this combination is used:
Machine Tools and Processing
- CNC Machining: FATEK servo drives with high-precision control ensure accurate movement of cutting tools (e.g., milling machines, lathes) within CNC machining centers. This allows for precise machining of complex parts with consistent quality.
- Robots and Pick-and-Place Systems: Servo drives paired with Servo Studio SD3 software control robotic arms for precise positioning and material handling within automated assembly lines or robotic packaging systems. This enhances productivity and reduces manual labor needs.
Production and Converting Industries
- Packaging Machinery: FATEK drives manage conveyor belt control, product feeding, and precise positioning tasks like labeling or sealing within packaging lines. Studio SD3 Fatek facilitates configuration and real-time monitoring for smooth operation and efficient product packaging.
- Textile Machines: Servo drives with Servo Studio SD3 Fatek software control fabric movement, tension, and cutting operations in textile manufacturing. This ensures precise handling of delicate fabrics throughout various processes like weaving, knitting, and finishing.
- Printing and Converting: The combination controls precise web tension, material feeding, and cutting operations in printing and converting machinery. This ensures consistent print quality and accurate material handling throughout the web processing stages.
Communications
FATEK VIETNAM COMPANY
Website: https://fatek.com.vn/
Hotline: 097 523 9823